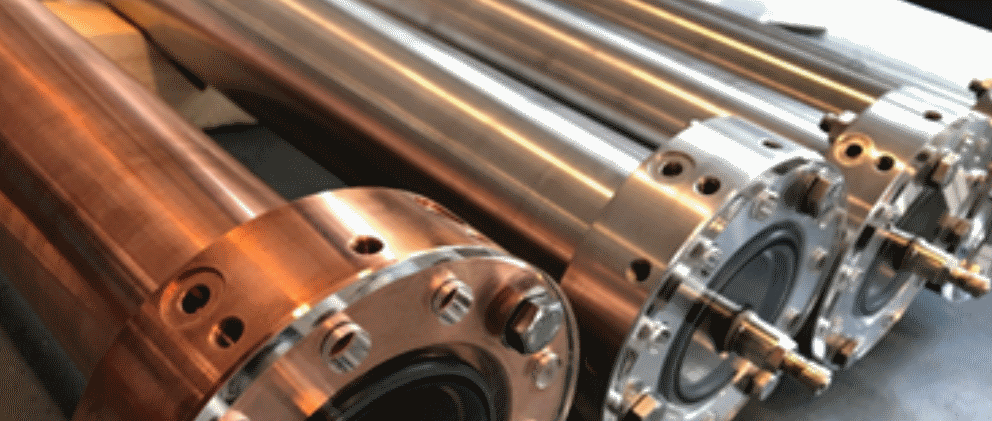
Precision Swiss-German consortium manufactures prototype corrugated waveguides for the ITER fusion reactor
2019
A precision Swiss-German manufacturing consortium led by Tiefbohrbär GmbH has developed prototype corrugated waveguides for the ITER fusion reactor that will be used to deliver microwaves into the hot burning plasma inside the reactor. The Tiefbohrbär consortium has manufactured waveguides in stainless steel, aluminium alloy and chromium-zirconium bronze and has been responsible for the required R&D for the high precision boring of the waveguide tube, the corrugation tooling and machining process, and a dedicated corrugation measuring system. |
![]() |
The temperature of the gas inside the ITER fusion reactor must reach 150 million degrees Celsius in order to reach the plasma state needed for the fusion reaction to occur. The fusion reactor will rely on three sources of external heating. One of these is the Electron Cyclotron Resonance Heating system which generates microwave beams at high frequency to initiate each plasma burn, contribute heating power to the plasma, and suppress certain types of plasma instabilities where plasma current is lost and energy content degraded.
Manufacturing high precision corrugated waveguide prototypes A manufacturing consortium led by Tiefbohrbär GmbH working with BGTB GmbH in Dortmund, Germany was awarded the contract to develop prototype waveguides by Fusion for Energy (F4E), the organisation managing Europe’s contribution to the ITER project. The consortium provides highly specialized deep drilling and bore shaping capabilities, and was able to provide all of the machining, tooling and measuring equipment required by the project.
The Tiefbohrbär consortium manufactures waveguides in stainless steel, aluminium alloy and chromium-zirconium bronze and is responsible for the required R&D for the high precision boring of the waveguide tube, the corrugation tooling and machining process, and the dedicated corrugation measuring system.
|
About Tiefbohrbär GmbH Tiefbohrbär GmbH performs precision deep drilling for high tech applications and is renowned for the smallest, the most unique and the most multifunctional deep drillings in the world. Deep drilling is the process of drilling deep holes where the drilling depth reaches more than 10 times the drill diameter, and Tiefbohrbär is able to drill deep holes with drilling diameter 0.5 mm to 250 mm up to 6000 mm depth with small tolerances and high quality surface finish. Manufacturing procedures and processes are certified to ISO 9001:2000 and ISO 13485:2003.Deep drilling is the process of drilling deep holes where the drilling depth reaches more than 10 times the drill diameter, and Tiefbohrbär is able to drill deep holes with drilling diameter 0.5 mm to 250 mm up to 6000 mm depth with small tolerances and high quality surface finish. Manufacturing procedures and processes are certified to ISO 9001:2000 and ISO 13485:2003. With 80 of the newest generation workstations (spindles) the company drills parts for ophthalmology, dental technology, implants and surgery, aerospace, microtechnology, solar energy, machine tools and molds, vehicle and marine engines. The company was founded in 1996 by skilled toolmaker Markus Bär and his spouse Carmen Bär. About BGTB GmbH BGTB GmbH in Dortmund Germany is a consulting company for deep drilling and machining with its main expertise in the development of cutting technology capable of machining non-cylindrical deep holes and chambers in metal parts. ![]() Roland Piehl
Project Manager / Sales Tiefbohrbär GmbH Lehenweg 15 CH-4852 Rothrist Switzerland This email address is being protected from spambots. You need JavaScript enabled to view it. |